Best Practices for Security Installers
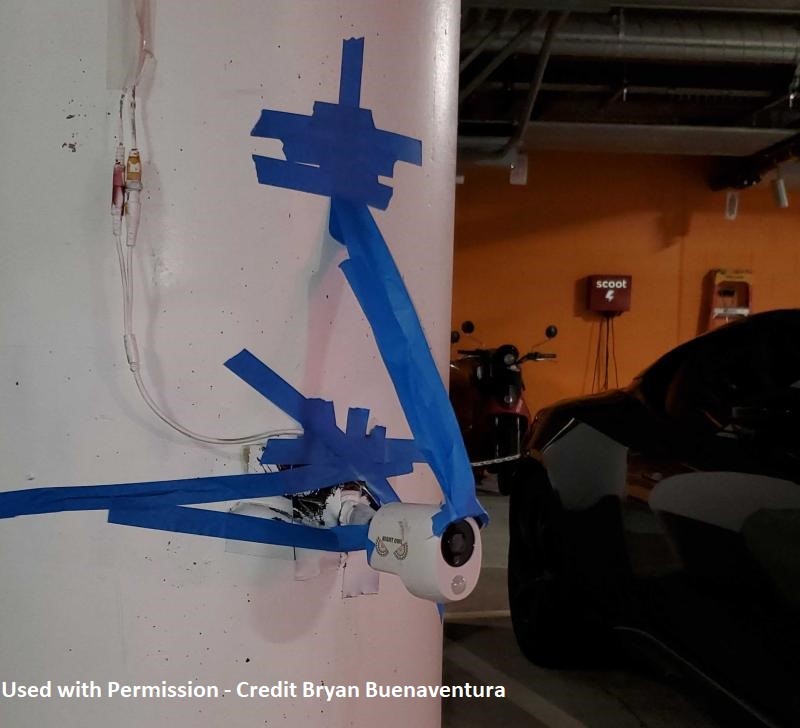
By: Jon Polly | Jun 30, 2020
Spend any time on Facebook or LinkedIn in a security integrator group and you can find pictures tagged with #cctvfail. While some are funny, and others cause you to scratch your head, the real truth is that someone was paid to install that camera. Their work is a reflection on the installer, which makes these installers look bad. The work also reflects on the integrator’s brand. Poorly installed equipment becomes an eyesore with the Integrator’s name attached. Poorly installed systems also tend to create service nightmares. For recurring revenue, security installation companies should be selling maintenance contracts, but these contracts should be more of an insurance policy. If a poorly installed system results in a large number of service visits, the customer will eventually get fed up and find another installer. Repeated truck rolls also cut any recurring revenue and can lead to a loss of revenue.
Safety First
First and foremost, on any job you should be safe. I’ll admit I have stood on the top step of a rickety 12’ ladder to drill holes. We have all done something unsafe in our career. If it is unsafe, stand up and say no. If you die because of an accident, your family will suffer the consequences of that mistake for the rest of their lives. Similarly, if you are seriously injured, no amount of money will bring back your previous life. Integrators should have some sort of OSHA training – either an OSHA 10 or 30 course, or a training conducted in-house. You should be safe at work and act as if OSHA is looking at your installation. Use equipment as intended and if it is damaged, pull it aside and either get it fixed or toss it.
Slow is Fast, Fast is Slow
If you have ever spent time at a gun range, you may have heard the range master say the words “Slow is Fast, Fast is Slow”. Slow and smooth keeps you on target. Fast may get you done quicker, but you will be back. When installing security equipment, this is true as well. Now, slow does not mean lazy. Slow means to take your time and do it right. Don’t rush the install. As a business owner, you should not be pushing the installer to rush. When you rush, you make mistakes. Things get damaged, warranty service on brand new systems increase, and both the integrator company and the end-user suffer. Now, there is no guarantee that a system installed with care will not have problems, but there is a much more likely chance it will have less problems over the lifetime of the system. Remember, the tortoise wins the race by working slow and steady.
Wire to the Code
Not every technician has an electrical license. But all should have a basic understanding of the National Electrical Code (NEC). While the code is updated with changes and additions, and even an occasional deletion every three years, a working knowledge of the code should be part of each installer’s work product. Wires coming out of knockouts with no Romex, wires tied to electrical conduits, and connections not made in a box are three of my biggest pet peeves. There are many other requirements that not only make the installation look good, but also keep the installation intrinsically safe and cut down on service issues. 120VAC conduit or cabling has a 60 Hertz Sine Wave; couple that with low voltage cable laid over flex or conduit, and the result can cause low voltage security devices to act strangely.
Install equipment as if the Authority Having Jurisdiction (AHJ) is standing right there. Many of us know the AHJ as the electrical inspector or the fire marshal. The AHJ is also the insurance carrier and the building owner themselves. If the Code requires a connection to be made in a box, put a box in. Junction boxes are minimal cost and should be associated with every job. If the sales person failed to cover junction boxes, don’t cover for him. As an installer, your work product reflects on your abilities and care, but also the Integrator / Installer’s brand. If enough jobs suffer because equipment wasn’t sold that should be, the sales guy will be reminded of how to make the project profitable.
Use the Right Tools
We have all wanted the left-handed cable stretcher at some point in our career. Each job requires the right tools in the tool bag. If the right tool isn’t in the tool bag, get it. Depending on the installer company, tools may or may not be provided. The right tool doesn’t mean the top of the line tool or the one that has a cool widget. The right tool is the correct tool for the job. You don’t turn screws with a hammer, and you don’t measure voltage with your tongue. Both are tools, but the wrong ones for the job. Some tools can be made and become the most relied upon tools. I have a reader cover removal tool / door contact tester made out of a magnet and a piece of fish tape. I have a piece of chain about 10’ long that when dropped down a wall with insulation goes quickly and pulls my wire to the appropriate spot. It cost me $3 and has saved hours of fishing walls. Find the right tools and make your life simpler. At the very least, you should have a good set of wire strippers, a voltage meter with a sounder, a multi-bit screwdriver, a measuring tape, and a level. Start there and build as the job requires.
Make it Look Nice
Seems simple right? A take on an adage, “Do unto others better than you would do unto yourself.” If you wouldn’t put something on your house the way it was installed at a customer’s site, make it better. Ever see a reader or camera that looks like a toddler installed it? Every installer needs a keen attention to detail; you should make each installation the best it can be. Sadly, installers are still guessing where the Americans with Disabilities Act (ADA)-mounted reader should be mounted. How many of us have heard someone say, “It goes about right here”? Devices get mounted on guesses, and at every door you have unique reader heights. If you do this, just hope the doors are not in a line. By the way, 36” above the finished floor (or in-line with the door knob) is typically acceptable.
If it is Wrong, Fix it
We’ve all seen the rat’s nest inside a panel. We’ve experienced the poorly installed (insert device name here) that screams “FIX ME!” How many of us have put a band-aid on the gaping wound and walked away? I’ll raise my hand and admit it. But this is also where we should take a moment and see that maybe an hour of time can be taken to fix the problem. As an installer, you may not be able to make the call. But call someone who can and give the reason to fix it. It’s probably not the last time you will deal with the headache.
Have a Work Mantra
As an installer, repeat in your head each day how you are going to do the installation. Repeat it until it sticks. Here are two I have used for years:
- “If a job is worth doing, it’s worth doing right, once, and only once.” How many of us like going back two and three times to work on the same job? I’m guessing no one is raising their hand here.
- “fix it (sometimes the easiest fix is the right one), if I have to go back; dig deeper, and if I have to go a third time, replace it all. There will not be a fourth time. “
Now come up with yours. That mantra will help you stay cool, calm, and collected if an installation is going sideways.
Step Away
We have all had the installation or service call that went sideways. How many have sat and read manuals on your phone sitting on a bucket in the IDF? Scratching our head as the fuse blows for the umpteenth time? The impenetrable wall that the sales guy said was easy to drill… Sometimes the best solution for the moment is to step away. Go get lunch. Stop looking at it for 20-30 minutes, come back refreshed, and the answer will probably be staring you in the face.
Have Joy
A friend of mine once described the difference between fun and joy: fun is fleeting, joy lasts forever. It is hard to have fun pulling the 800th wire, or being in a 140° attic. But when you do your best and put quality work into the world, you will enjoy what you do, even if it means going in the 140° attic.
I like how you said that a slow installation does not mean the workers are lazy but rather taking their time to get it right. I’d hate to get a security system installed only for it to be done wrong. I want my house completely protected, if that means they take longer to do it then they take their time.