Electrical Job Site Management in Four Easy Steps
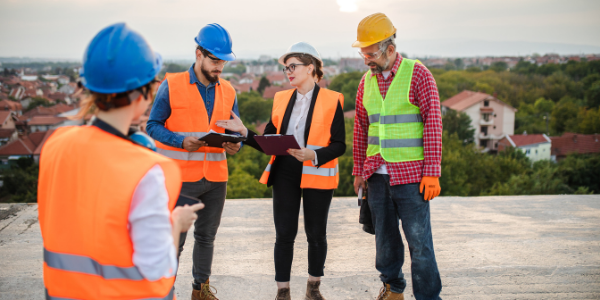
By: Dave Varga | May 05, 2021
By the time the company makes it to the job site, considerable time and money have already been spent on the project. The electrical foreman has many responsibilities and can single–handedly be the cause of a failed project. The foreman needs to be the National Electrical Code guru, assistant to the Project Manager, Human Resources liaison, team coach, and much more. Like other positions in the field, the electrical foreman needs continuous training to keep on top of the game. Here are four easy steps for managing an electrical job site.
Step One – Designate a Work Space
Regardless of the size of the job, you need a central location or office area to conduct your work. The space needs to be kept clean and organized. This area could be as simple as a space containing a six-foot table and a couple of chairs.
This area should contain the following items:
- Job hazard analysis (JHA)
- Sign–in/sign–out sheet
- Needs list
- Lockout/Tagout (LOTO) kit
- Personal protective equipment (PPE)
- Stock
- Caution tape
- First aid kit
- Job site rules
- Other company and job site–related items
Equipment and stock are needed for every job. The crew should be reminded to regularly update and maintain the needs list to include materials that need to be restocked, tools that are going to be needed, and even additional PPE. This list is very important for the foreman and should be promoted to the crew at the beginning and end of each day. One way of reminding the crew to update and monitor the list is to post it next to the sign-in/sign-out sheet.
The foreman should have a “Foreman Book” containing job–specific information. The book typically contains bid information, including all labor hours, fixture and gear information, supplier information, job schedules, and daily reports. A small portable and lockable hanging file folder system is needed to contain miscellaneous items such as human resource documents, safety documents, hazard communication documents, and more. Also, a laptop computer and portable printer are standard equipment on larger job sites.
Step Two – Avoid Injury
Injuries are bad for the company in many ways. Injuries negatively impact moral, profits, reputation, and even the project schedule. The goal on every job site is to avoid injury, period. The foreman must perform a job hazard analysis (JHA) with the crew before the work begins. The JHA can be documented on paper with eventual signatures from all crew members or on a white board. For larger job sites and those with six or more crew members, the white board is great for displaying job tasks, code related articles, and crew member teams. The white board also helps organize the workday and the job site. When it comes to safety, each employee must have the required PPE. The company should always have extra PPE on hand in case someone is missing their PPE or it is damaged. This is important to keep the day moving forward with no injuries.
Step Three – List Daily Work Tasks
The job site foreman must keep a list of work tasks on hand at all times. Often, a crew can finish a task early or run into an issue where a task cannot be started or completed. In order to not waste valuable labor hours, there should always be another task on deck and ready to go. If there are not extra tasks available each day, the crew size may need to be adjusted. A constant and logical flow of work keeps moral up. Lower moral can lead to a slower work pace. A good crew will keep the work pace up when they know there is plenty to do. The list of tasks should also be prioritized, with the most important task at the top. The list can come in handy when surprise manpower arrives or when manpower does not show up. Make sure the Project Manager (PM) or the second person in charge on site has a copy of this list in case the foreman is not reachable.
Step Four – Tools and Materials
Without the proper tools and materials on the job site you might as well shut it down. This is the most common moral buster and money loser. When the crew arrives each day, they are anxious to get the day going. A full day of work helps the day go by quickly and the week go by quickly. If the crew does not have the needed contractor–supplied tools, their progress comes to a grinding halt. When the crew has to share tools, tasks can take twice as long. Sharing contractor tools may lead to unnecessary site travel, visiting and talking, and other distractions.
Not having the required materials effects the job in the same ways. Over time, the crew can spend countless hours looking for materials when the materials are possibly not even on the site or just simply thrown on a pallet with no organization. The materials must be ordered days ahead of time and stocked with clear organization. Metal material carts on wheels are the best way to store materials. With good organization, it is easy to see what materials need to be restocked and it is easy to find materials needed for a task. When storing company tools in a full gang box, it is important to label the tool case on all four sides so it is easy to find the tool without having to pull out each case during the search. Last, make sure there are enough ladders of various sizes for the crew. Working on a ladder that is too big or too small is another way to lose valuable labor hours.
Site Managed
The steps above seem easy enough, but they are often overlooked on job sites. To have a successfully managed job site, the foreman must start with these basic steps. Following these steps will help keep the crew happy and productive, and it will be easier to change task direction at a moment’s notice. This simple organization will also allow more time for other important foreman roles. A weekly visit by an owner or project manager can help point out any deficiencies and keep the site successful and profitable.
Awesome! Something I really needed, duties of a foreman!