Developing Troubleshooting Skills for HVAC Technicians
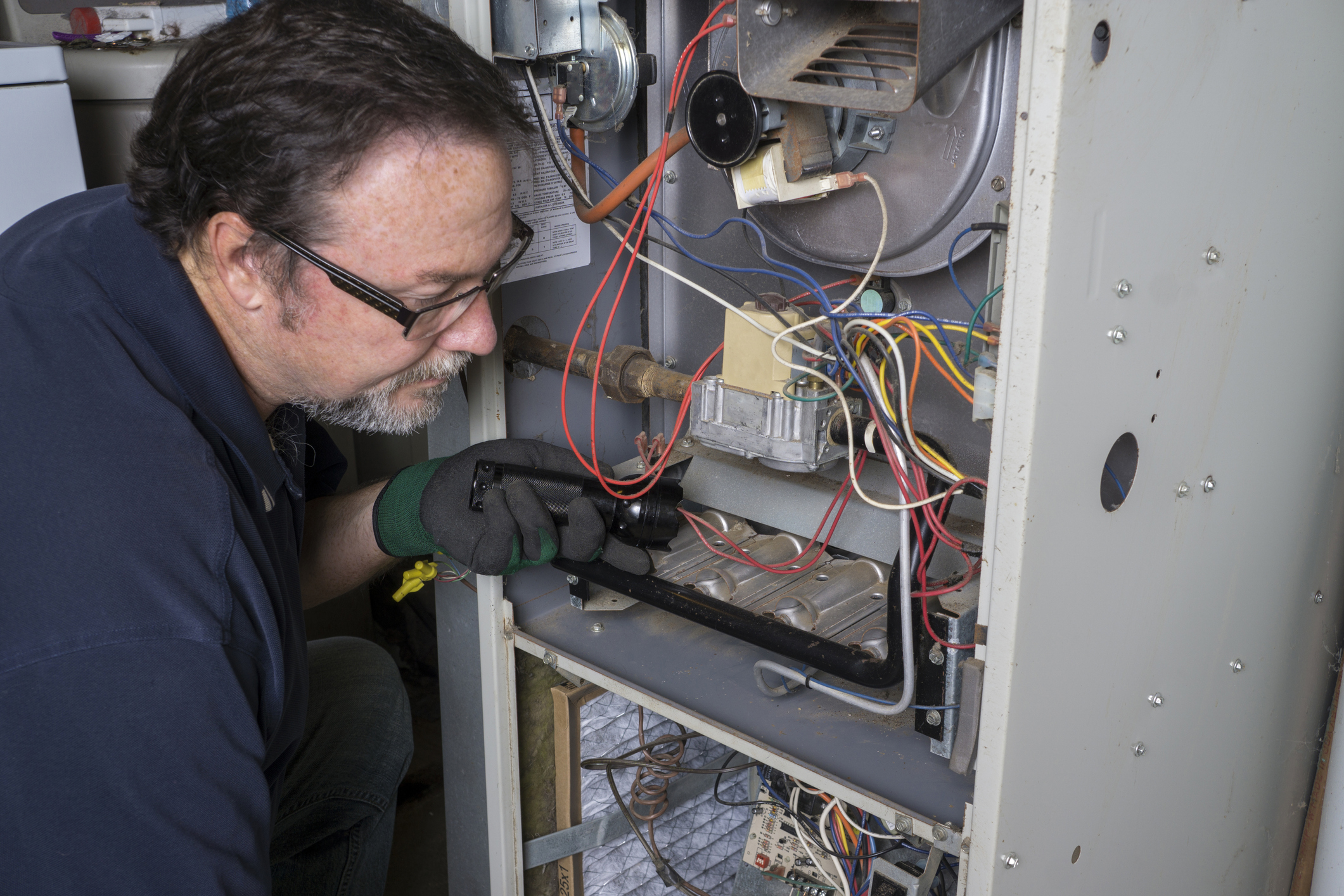
By: Gary B. Xavier | Jun 01, 2022
Troubleshooting of HVACR systems and equipment can often become a time-consuming, frustrating process, and teaching technicians how to develop their troubleshooting skills can be the same – time-consuming and frustrating.
Troubleshooting is a skill that can be learned, but because everyone learns and processes information differently, it’s often impossible to teach a HVACR technician the exact same method of troubleshooting that a senior technician or instructor uses so easily and successfully.
Though troubleshooting is a skill that must be acquired by each technician in their own manner, there are fundamental concepts that work for everyone, and they should be the foundation used to help teach technicians to become proficient troubleshooters.
The basis of developing troubleshooting proficiency begins with logical thinking.
Inductive logic, or inductive reasoning, leads to a conclusion based on observation and experience, which suits both the troubleshooting process and the technician’s abilities to learn and process information. This method of thinking takes specific information from observation and experience, and makes a broader generalization that’s considered probable, while remaining open to the fact that the conclusion may not be 100% guaranteed.
Beginning technicians, though, may lean towards using deductive logic rather than inductive logic, which usually leads to changing parts rather than truly diagnosing the problem.
Deductive logic, also called deductive reasoning, is the process of reasoning from one or more statements to reach a logically certain conclusion. This type of thinking will not work successfully in developing troubleshooting skills, as there are too many variables in working with HVACR systems.
Developing inductive thinking in HVACR technicians results in more effective troubleshooting of system problems and can be accomplished by building a foundation of logical thought processes.
The following five steps are a proven, reliable method of learning to troubleshoot HVACR systems:
1) OBSERVATION
Observation sets the tone for how a technician approaches the problem, forcing them to look at the big picture, pushing them out of parts changer into troubleshooter mode. The approach includes looking for obvious things to help in diagnosis.
Observation includes collecting data on the system’s history. Is this problem just beginning, or has the equipment been performing erratically in the past? Discussing the system operation with the building owner or tenant is a critical part of the observation process. Look for the obvious: start with the thermostat setting – is the unit calling for heat or cooling?
If the unit is not operating at all, start with the electrical supply and work from there. If the unit is operating but not performing properly, then start by determining exactly what the system is doing incorrectly. Look before you touch.
2) LOGICAL THINKING
Using the data leaned from observation, the technician should then begin to think logically through the problem. Inductive logic uses the observation information combined with the technician’s experience in similar situations to determine a probable cause of the problem.
If it’s an air conditioning issue, technicians should mentally review the refrigeration cycle and the steps involved in transferring heat. If it’s a heating system, they should think about the fuel supply, the process of changing energy from fuel to heat, and the sequence of ignition for the burner.
Logically thinking through the problem and the possible cause before reaching a conclusion is a critical step in developing good troubleshooting skills. Think inductive, not deductive!
3) ESTABLISH A PATTERN
One of the easiest ways to make errors in troubleshooting is to miss a critical step in the troubleshooting process. Once technicians have developed the process that works for them, they should repeat the same pattern of troubleshooting in every situation.
Do not deviate from the pattern. If the logical thought process points a technician to always start at the thermostat, then do that every time. Following the same pattern every time will eliminate missed steps and streamline the troubleshooting process.
4) ACCEPT HELP
Technicians should never feel that asking for help is a sign of weakness in their troubleshooting capability, it is, rather, a sign of strength. No one knows everything about every situation and asking for help is a surefire way to increase their knowledge. The help may come from many sources, not just from an instructor or fellow technician. Discussing the system operation with the resident or maintenance person during the observation phase is one method of gaining valuable help.
Manufacturers and distributors are often an excellent source of information, as they want their equipment to perform properly. Every manufacturer provides written troubleshooting guides that are provided with the equipment, and these guides are a reliable, practical source of information. If contacting the manufacturer or distributor is necessary, the internet is a rapid way of doing so.
5) PRACTICE, PRACTICE, PRACTICE
Repetition is key to becoming a proficient troubleshooter. Even after decades of practice, a technician may not have seen every type of system or experienced every problem. Equipment is constantly changing, especially the controls, so a technician must constantly study to become familiar with new equipment, as well as improvements in diagnostic tools and practices.
Troubleshooting is a skill that needs constant practice, and fine tuning, to retain its proficiency. Following these five steps is a way to help make troubleshooting excellence a reality.