Basic Surface Water Treatment
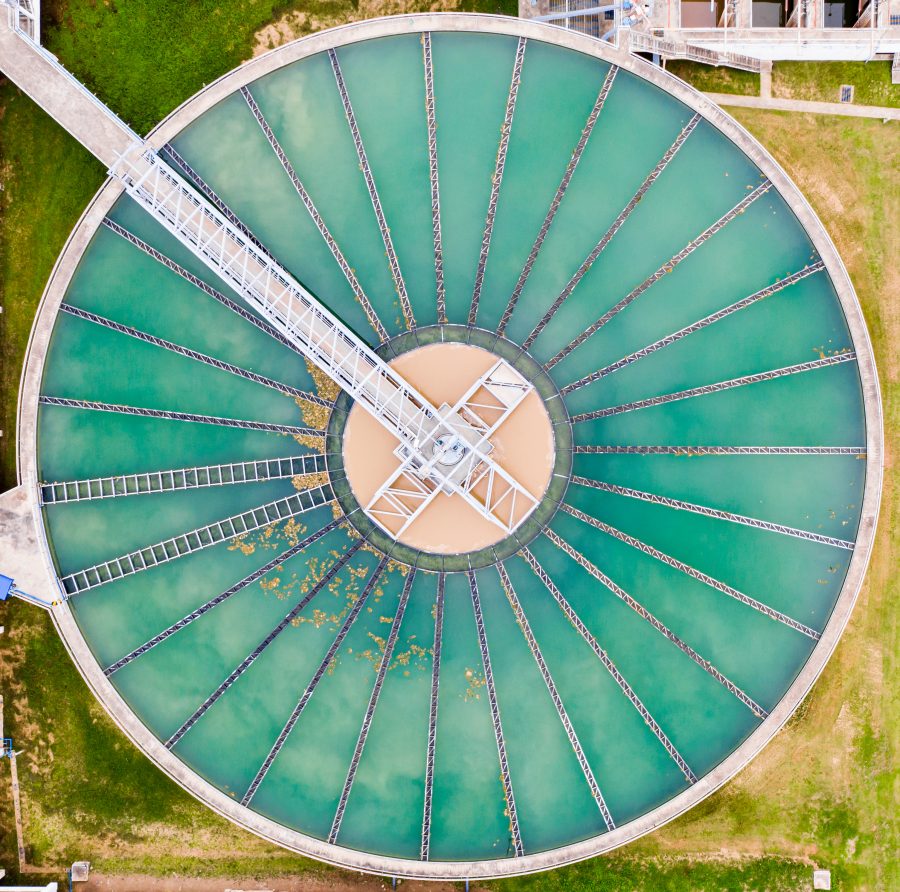
By: Steven Lambert | Jan 06, 2022
Surface water treatment is used to prepare water collected from streams and lakes for human and industrial consumption. The chief mission is to protect human health, eliminating harmful organisms and chemicals before the product is distributed. The facilities used have had different names over a couple of centuries and some of the ancient names are still used today. Some names indicate limited capabilities by using words such as filtration plants or treatment plants. The best term may be purification plants, indicating complete success.
Consider first the raw water supply: The stream or lake providing the water for treatment. The source water should be as pollution-free as possible. Any problems must be addressed by treatment, or better, getting control of the sources of pollution and eliminating them.
The supply must deliver ample volume to meet system needs. Regulations set how much water can be withdrawn, especially during drought conditions. If system requirements cannot be met, the source must be rejected and another developed.
The raw water enters the plant and coagulants/flocculants are added to impart a positive charge to some of the particulates (turbidity, or “mud”). Aluminum Sulfate (Alum) and Ferric Chloride (Ferric) are choices, among others, for this purpose. The resulting reaction is that positive, negative, and balanced charge turbidity will attract magnetically to one another, making larger and heavier particles that rapidly settle filter easily into clear water.
An alkaline chemical, such as lime or caustic soda is used to provide the alkalinity requirements for the flocculent to form a more solid floc, preventing the concentrated material from degrading back to its more natural state. In the past, chlorine was added to sequester iron and manganese and begin disinfection. This practice still exists but is out of favor due to the possible formation of disinfection byproducts, which have been found to cause cancer.
Once added, these chemicals are quickly mixed with a flash mixer to begin coagulation. Then, the water flows into the flocculators(s), which slowly mix the treated water to increase the size of the coagulated floc by allowing them to form larger particles as they collide with one another and “stick” together. At this point, flow velocity is extremely reduced to allow time for floc to form to the maximum size. These larger and heavier particles flow into the sedimentation basin(s).
At the same reduced velocity, without mixing, the floc is allowed to settle to the bottom of the sedimentation basin(s) as water travels their length toward the filters. Most of the floc will be captured at the sedimentation stage before filtration. The water is visibly clearer. These three stages of treatment convert unfilterable silt into a filterable floc. Pre Chlorine is added prior to filtration for initial disinfection and metals control.
At the filter influent, settled water is received at the same low velocity. The water flows downward through the filter media, usually consisting of a top bed of coarse coal particles supported by a bed of filter sand. This provides ready passage of water through the filter(s). The lighter coal remains on top of the sand. Coarse material on top renders better filtration. Sand captures the finer particles.
Filtered water has the clear look one wants. Raw water containing a few or up to hundreds of turbidity units (Ntu) has been converted to only a small fraction of turbidity at less than 0.1 Ntu, usually at the levels of 0.05 Ntu or less.
Post Chlorine is added to bring the concentration up to ensure disinfection through storage, distribution, and consumption, preventing the chance of waterborne infections by nearly 100%.
Post caustic soda or lime are added to raise the pH and alkalinity levels to a slightly alkaline state (pH between 7.0 and 8.0 and alkalinity above 18 mg/L}. This makes water less corrosive, reducing pipe corrosion, preventing metal poisoning by lead and copper.
A corrosion inhibiter, usually a phosphate product, is added to prevent the chemistry of corrosion from taking place.
Fluoride is added to promote dental health, hardening tooth enamel.
Our product is now complete. The veteran operator will judge this description of the process too simplistic. To the novice, it provides a map for success. The devil is in the details. Every level of the process requires the proper dosages of each chemical to achieve success. The Operator must be proficient in basic lab skills and setting the dosages lab results indicate.